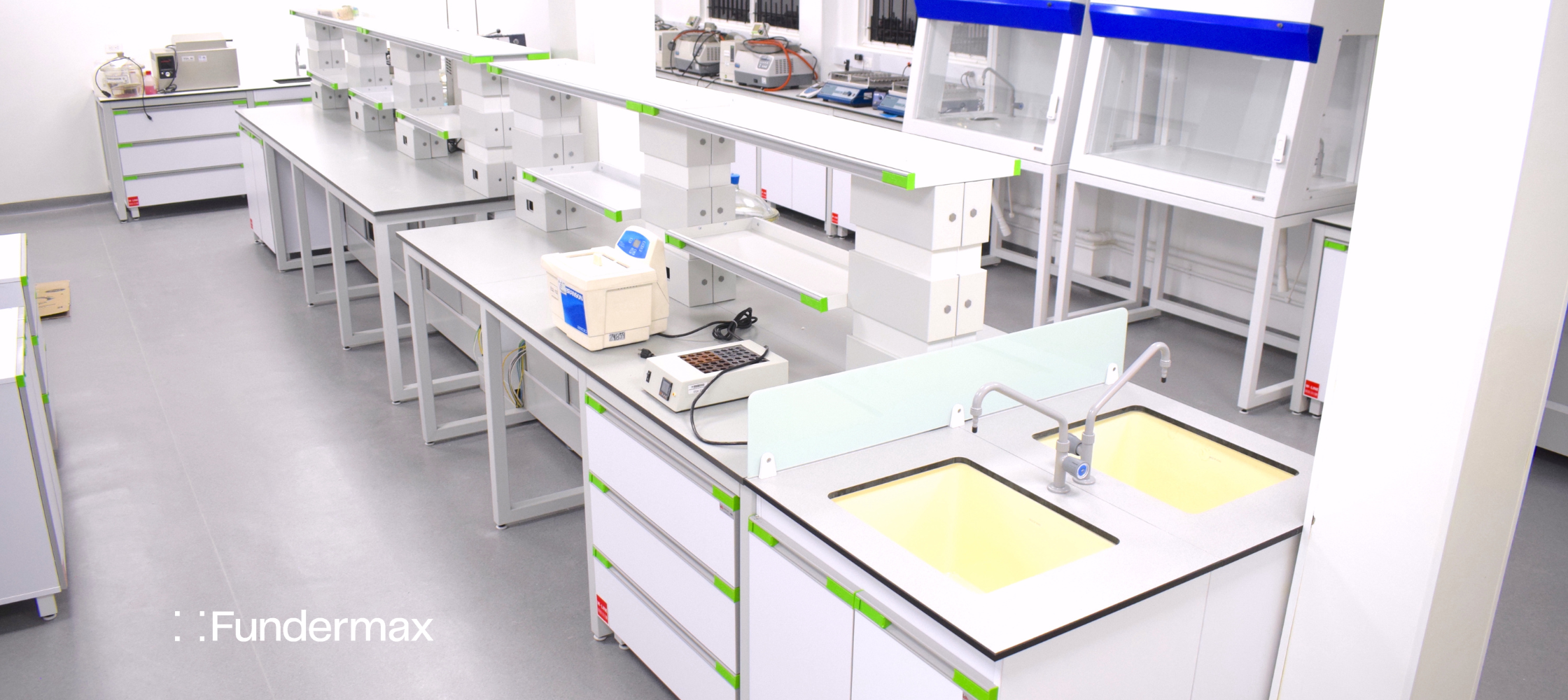
Sustainable Lab Design
Sustainability in lab design has historically focused on operational efficiency (energy usage once a lab or building is occupied). However, the need to reduce carbon emissions is growing and urgent. This has understandably widened the scope of green laboratory practices to include more than just operational efficiency. Materials used in construction should also be considered for their sustainable impact.
Yet, sustainable design should not require a reduction in quality or durability – or even increased cost. Through this blog we will take a deeper dive into the embodied carbon of construction materials with emphasis on lab work surfaces and furniture.
Flexible Focus
Lab design is an art. Professional lab planners, designers, and architects understand the heavy demands on lab spaces and on the variety of materials used. Alongside the continuing need for more flexible and adaptable solutions, we all face the need for sustainable building design.
When discussing sustainable building design, lab planners and designers have primarily focused on the building use, once occupied. This is to be expected, as labs are heavy users of energy with fume hoods, HVAC systems, lighting, and equipment. These concerns have been widely recognized and addressed as building energy performance standards have been implemented, and some local authorities are even beginning to issue fines for noncompliance.
However, the sustainability of the materials and furnishings used in lab spaces should not be overlooked. There is a great opportunity to broaden a green lab initiative by recognizing that sustainability not only refers to the ‘greenness’ of a product but also to its durability. Choosing durable materials that will stand up to daily activities and exposures will reduce the potential for early replacement and therefore reduce waste too.
Evolving Lab Design
Consider how the design of labs are evolving with the traditional wet lab becoming drier through the advent of AI and more computer connectivity. Additionally, with modern science seen more as a social activity to enable collaboration, today’s laboratories (and in particular, the areas surrounding them) are being designed as social spaces that nurture interaction and collaborative, team-based research.
With the need for adaptable and flexible solutions, the question arises: is it truly possible to ‘future proof’ design? And, particularly when designing builds for S&T hubs, how do you accommodate today’s needs and those of the short – midterm future, all while ensuring sustainability? Consider, for example, the increasing interest in Mass Timber Buildings and of course, the imperative need for anti-vibration in lab design.
Here is where we believe the need for lighter-weight, sustainable, adaptable, yet highly durable materials take center-stage. (And on top of that, the utilization of materials that are manufactured sustainably without compromising durability.)
Lab work surfaces are a perfect example of an application that must withstand harsh usage and provide longevity – all while maintaining that just-installed appearance and performance.
Meeting Directives to Reduce Emissions
The need for sustainable design arises from the overarching need to reduce carbon emissions. The focus of global directives to reduce greenhouse gas pollution by 2030 and 2050 continues to be on the completed and occupied building environment. While this is of course very important, it is also increasingly important to consider the efficiency of the extraction and manufacture of construction materials – particularly if we hope to meet the Net-Zero requirements as outlined by the IPCC. With this in mind, we turn our attention to the construction of buildings and the manufacture of the construction materials, with an emphasis on the interior of laboratories.
What is Embodied Carbon?
Sustainable buildings should reduce carbon emissions in all forms, as much as possible. When most people hear “carbon emissions,'' they think of operational carbon. But, we must also consider what is called embodied carbon. “Embodied carbon will be responsible for almost half of total new construction emissions between now and 2050.”[1]
Embodied carbon refers to the greenhouse gas emissions (or GWP – global warming potential) arising from the extraction, manufacturing, transportation, installation, maintenance, and disposal of building materials. Embodied carbon represents a growing percentage of global emissions and requires urgent action.
Canadian Architect reports that between now and 2060, the building industry is expected to more than double the number of buildings we currently have on the planet! Material choice can and will have a huge impact on the embodied carbon emissions associated with the building industry.
When analyzing the implications of embodied carbon, consider the carbon emissions generated through material production, transportation and installation. The amount of energy used in those processes (known as embodied energy) and the fuel used to provide that energy is also factored into determining the embodied carbon – which is calculated from the carbon intensity of each energy source.
Generally, the higher the embodied energy, the higher the embodied carbon. But, there is a caveat to that – as more processes become more sustainable, the carbon intensity of power generation decreases, and the two can become disconnected.
The image below illustrates the Key Life Cycle stages of a building. Gray represents embodied carbon, and blue is operational carbon.
Note that material manufacturing, transportation to site, and the construction process result in a “carbon debt” before day one of operations. Until recently, it hadn’t been considered in most green or net-zero buildings policy, design, tracking, or reporting.
This disconnect is particularly surprising considering that the term “embodied carbon'' is aligned with the carbon footprint associated with building materials. Additionally, according to data from UNEP’s 2019 Global Status Report for Buildings and Construction Sector, the building sector is responsible for 39% of global energy-related carbon emissions, 11% of which comes directly from the embodied emissions of new construction. The impact of embodied carbon on a building’s carbon footprint is clear.
Does it Matter?
Some may argue: “Only 8-11% of global emissions result from the manufacturing of construction materials. Is it reasonable to focus heavily on embodied carbon?”
Yes.
Embodied emissions will continue to increase due to an increased global demand for construction materials and a decrease in relative proportion of operational emissions from building operations as building energy efficiencies continue to improve. Giving our attention to the environmental impact of construction materials is warranted.
When selecting materials, remember that plant-derived materials store carbon dioxide the plants have absorbed during their growth (recall your photosynthesis lessons). In other words, plants capture and store atmospheric carbon (this is also known as sequestration of carbon). Whether this stored carbon remains stored in those plant-derived materials depends on what happens to the materials at the end of the material’s life cycle.
Life Cycle Assessment
The Life Cycle Assessment (LCA) is a scientific tool used for evaluating environmental effects of products or services throughout the complete life cycle, “from cradle to grave”. The life cycle includes the extraction of raw materials, refining, fabrication, transportation, use, recycling and disposal of the product, as well as the energy and ancillary materials supplied. An LCA provides you with a chance to see the bigger picture of how a material impacts the environment.
Measuring and quantifying embodied carbon has become easier to understand through the LCA, the primary stages of which include:
-
Product (A1-A3) – includes extraction and upstream processing of materials, transportation, and manufacturing impacts
-
Construction (A4-A5) – includes transport to the site
-
Use (B) – includes maintenance and replacement
-
End-of-life (C) – includes demolition and disassembly as well as waste processing and transportation
-
Beyond the life cycle (D) – includes potential benefits from reuse, recycling, and/or energy recovery
Measuring Carbon Footprint
Having identified the life cycle, the assessment should then focus on greenhouse gas emissions, including carbon dioxide, which are added up over the product’s life cycle and reported as GWP (global warming potential). GWP is expressed in carbon dioxide equivalents (CO2e). This is an agreed-upon definition for expressing a product’s carbon footprint.
To enable an agreed upon methodology for measuring effectively and calculating the embodied carbon of products it is imperative that a consistent scheme is used. For Green buildings and construction products, the Environmental Product Declaration is the agreed-upon tool and methodology for disclosure and transparency.
For example, as phenolic panel manufacturers, we can measure and highlight how to reduce the environmental impacts of our products through publicly disclosed EPDs. Building designers can then use these LCA-based EPDs to determine the carbon footprint and overall environmental impact of a whole building. From there, architects can search for ways to reduce life cycle greenhouse gas emissions and other impacts through strategies like
-
Ensuring efficient use of materials (i.e. “right-sizing”),
-
Selecting materials with more efficient manufacturing processes,
-
Minimizing transportation impact through use of local materials,
-
Using robust materials that require less maintenance, repair, and refurbishment,
-
Choosing materials that can be reused or recycled instead of landfilled.
Material transparency through EPDs is vital to sustainable building design, lab specific or not. Particularly in a green lab initiative, though, the opportunity to reduce carbon emissions remains large from both an operational efficiency standpoint and from a consideration of embodied carbon when choosing materials. A forthcoming article will take a closer look at how material transparency can play a fundamental role in true sustainable design.
From lab work surfaces to wall lining and more, Fundermax is committed to sustainability – and has been for more than 100 years. Throughout all of Fundermax operations, we are dedicated to creating and implementing measures to continuously reduce environmental pollution and increase energy efficiency.
If you are designing a laboratory space, our experts are available to discuss the unique qualities of our phenolic panel lab surface technologies. Pulling from our experience in various laboratory applications around the world, our team can help support your sustainable lab design, ensuring it leverages green laboratory practices and is suited for superior performance. Contact us today for more information.
[1] https://architecture2030.org/embodied-carbon-actions/