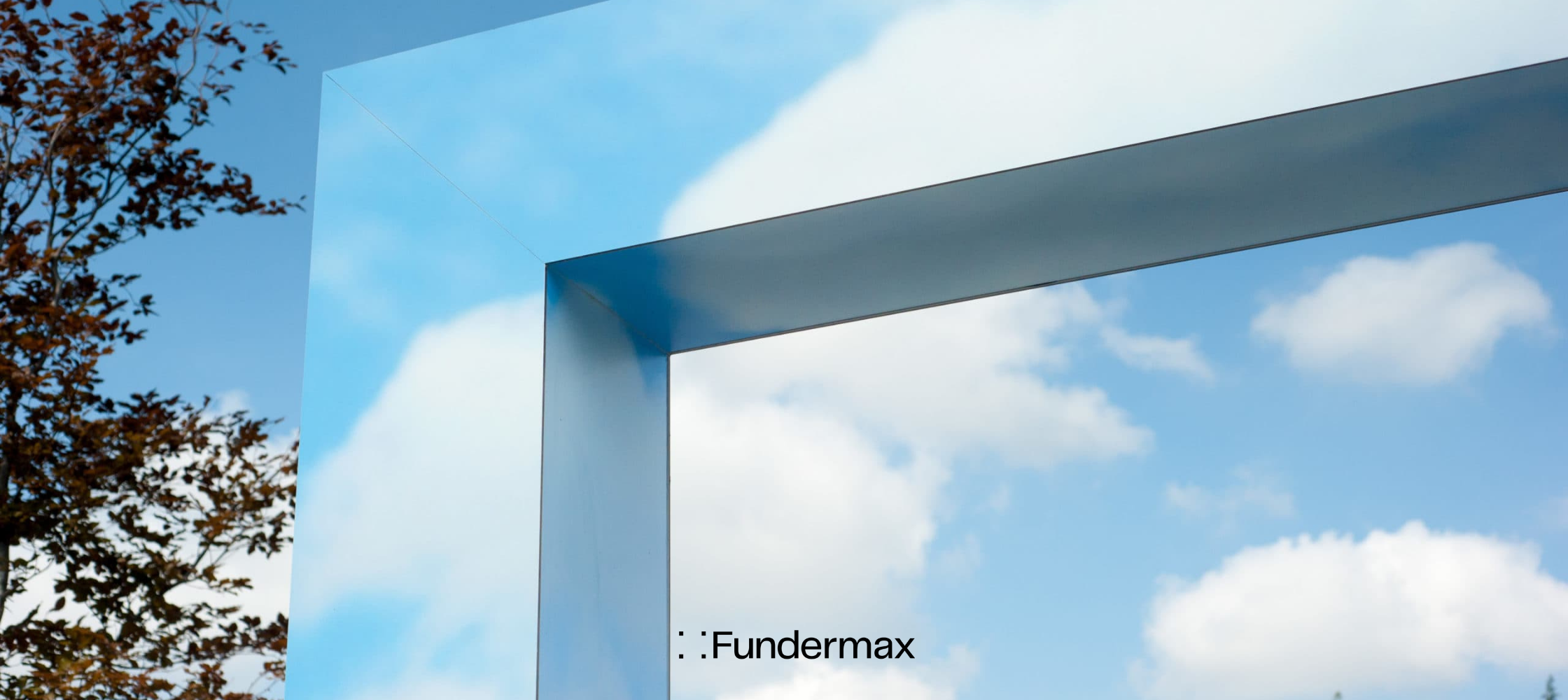
Delamination is a Thing of the Past with HPL Panels
Unfortunately, when most people think of laminates, they think of laminate panels delaminating. We can all picture the peeling countertop or the bubbled floor.
Whether a laminate product delaminates because of regular use over time or from intentional vandalism, it is a constant headache for the maintenance team and an absolute nightmare for the person watching the budget. It’s also a disappointment for designers and architects who know their design will be short-lived thanks to a material that is just not made to last.
But, there is good news for architects, designers, and building owners alike. Very good news. Delamination is 100% in the rearview when you specify quality high-pressure laminate (HPL) panels. At Fundermax, we are thrilled that we can offer absolute assurance that our HPL panels will not delaminate -- ever. How? We are so glad you asked.
What are HPL Panels?
HPL stands for high-pressure laminate. HPL panels are often called phenolic panels, and the terms may be used interchangeably (the basis of most high-pressure laminates is phenolic resin).
HPL panels are made using high pressure and heat to compress layers of kraft paper impregnated with thermosetting resins. This results in solid, compact boards that are durable, long-lasting, and virtually maintenance-free. You can refer to this article for a more detailed, step-by-step review of how phenolic panels are made.
(Phenolic cladding panels are also sustainable materials that can help satisfy green building requirements. See this article for more information about HPL and sustainability.)
What Causes Delamination?
Delamination happens when the top laminate layer separates from the laminate panel. This is exactly what most people picture when recalling that peeling countertop edge.
But what architects know is that while the general population may picture delamination on a small scale like a kitchen countertop, delamination can happen on a much larger scale when using an inferior laminate wall panel system.
Laminate panels can begin delaminating as early as when the installer drills into the panel to anchor it to the wall. At that point, moisture can begin penetrating the interior layers of the panel. Edge treating is immediately required to avoid moisture penetration. This is all in an effort to avoid delamination, but success is never guaranteed.
Consider the example of paint chipping or peeling on a car. The top layer or seal and the paint have delaminated and resulted in the peeling, cracking, and chipping you see on the surface. The surface must be tended to with great care and regular maintenance to avoid total deterioration.
What are the Risks of Delamination?
-
Separation and exposure of the panel core
-
Finish discoloration
-
Overall panel discoloration
-
Cracking, peeling, and bubbling of the panel and finish
-
Swelling around panel edges and screw holes
-
Moisture collection
-
Compromised protection from UV rays and weather exposure
-
Shortened product lifespan
-
Added costs for panel replacement and increased maintenance
Do HPL Panels Delaminate?
While the overall makeup of HPL panels is similar across different phenolic panel manufacturers, each has its own process and makes their panels differently based on various factors.
One unique feature of the Fundermax process is our in-house resin station. We mix and prepare our own resin formulas onsite which allows us to achieve the chemical quality required to ensure an industry-leading product. Fundermax owns several patents on the technology we use with the highest quality press technology.
Fundermax compact HPL panels go beyond “little to no risk of delamination.” Fundermax HPL panels have eliminated the risk of HPL delamination.
Our panels do not delaminate; when they come out of the press, the final product is a non-porous, homogeneous material. That means there are no longer separate layers, so there is nothing to separate or delaminate.
Delamination and phenolic panels simply do not go together at Fundermax. (And we stand behind this by offering an industry-leading 10-year warranty, including labor.)
What Makes HPL Panels so Durable?
The durability of HPL panels begins with how they are made. The kraft paper core of phenolic cladding panels is made of natural cellulose fiber composed primarily of wood and impregnated with thermosetting resins. (Leading phenolic panel manufacturers, including Fundermax, source these raw materials from vendors certified by the FSC and/or the PEFC.)
Then, high heat and pressure is used to cure the resin-impregnated layers (including the visible decorative layer). The resulting material is a nonporous, weather-, UV-, and chemical-resistant material that does not fade, chip, peel, or delaminate and is able to withstand harsh cleaning when necessary.
Beyond the exceptional durability of HPL panels is the design freedom available. Designing with an abundance of panel colors, woodgrains, finishes, and mounting options takes on even greater life when it’s combined with the assurance that HPL delamination will never be an issue.
Contact Fundermax today to discuss whether a phenolic wall panel system may benefit your next project.