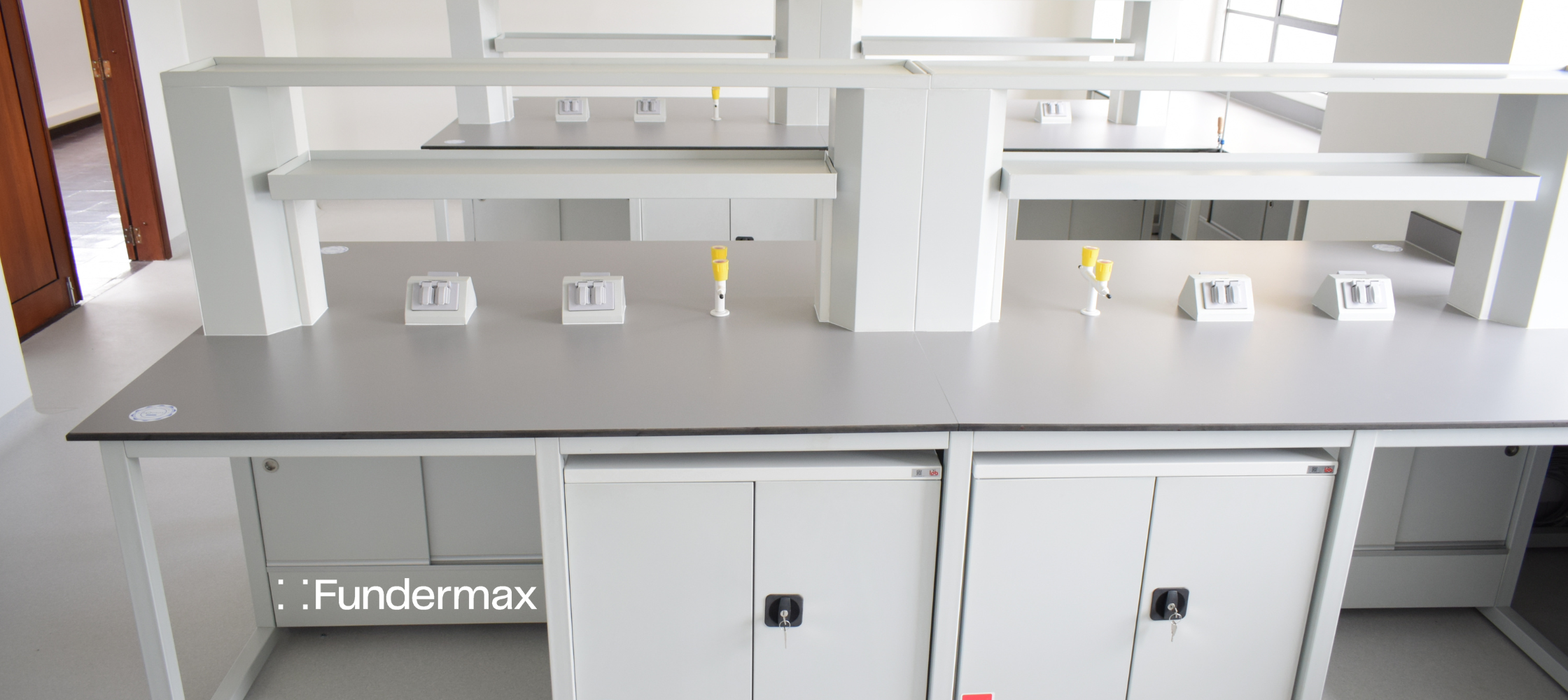
Material Transparency: EPD & HPD
Material transparency is fundamental to designing sustainable labs. Fundermax has been committed to sustainability for more than 100 years, and we are dedicated to providing and advocating for material transparency.
Through Environmental Product Declarations, Health Product Declarations, and more, designers and planners can be confident that their material selections are aligned with their efforts to design sustainable labs.
In this article, we will discuss EPDs, HPDs, and the importance of material transparency.
What is an Environmental Product Declaration (EPD)?
According to the EDP Registry, “Environmental Product Declaration (EPD) certificates are independent declarations that quantitatively evaluate and declare the environmental performance of a product or service, as described in ISO 14025, on the basis of the principles of ISO 14040 Life Cycle Assessment (LCA) standards.”
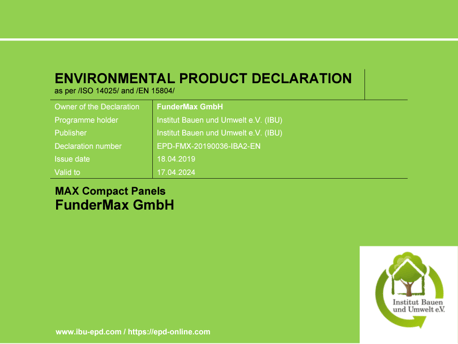
Put more simply: an EPD is a “nutrition label” for a product’s environmental footprint. However, just like with a food nutrition label, it helps to know what you are looking for. It is also important to remember that looking at an EPD on its own is not sufficient to tell you whether or not a product is “good for the environment.”
EPDs are publicly disclosed documents, so they are readily available to those who know to look for them. Sites such as Mindful Materials, for example, allow those registered to download these documents. Nevertheless, we believe it is still incumbent upon the manufacturer to provide you with an EPD.
How to Effectively Compare Environmental Product Declarations
As with most data, it is valuable to make comparisons between materials. However, using EPDs to compare materials will only be effective if the following standards are comparable:
Functionally Equivalent Products
Functionally equivalent products have the same unit size (such as ½” thick and 1 SQF) and technical performance. Technical performance characteristics vary by product category and use. For example, performance characteristics of a material may include things like use (commercial vs. residential), durability (density, etc.), or in the case of phenolic resin panels, whether they are lab grade or commercial. For instance, you can’t compare an EPD of a concrete block with a carpet tile.
Note that determining functional equivalence involves judgment and assumptions, and it must be done with care.
Once the functional equivalence of the products being compared is established, it is also key to ensure that each Environmental Product Declaration has the same:
Methodology
The EPDs should follow the same Product Category Rules (PCR). In other words, PCRs are meant to be objective and serve as the guidelines for life-cycle assessments (LCAs), which in turn inform the EPD. Perhaps even more importantly, they help promote fairness by ensuring that all the products of the same type are measured with the same yardstick.
System Boundaries
The EPDs must include identical life cycle stages. Life cycle stage reporting varies, and the reported stages must be the same (i.e. cradle-to-gate analysis cannot be compared to cradle-to-grave).
Upstream Data
Life cycle inventory datasets for transportation and electricity generation should also be aligned.
Industry-Wide EPDs as Benchmarks
As with most materials, there are many industry-wide EPDs, and there are product- and manufacturer-specific EPDs. Having an industry benchmark can provide an additional layer of comparison to independent product data, particularly as many manufacturers place differing emphasis on sustainability in their manufacturing processes.
For example, a good benchmark for phenolic resin panels comes from the ICDLI (International Committee of the Decorative Laminates Industry). If you consider this data and then compare individual phenolic panel manufacturers (like Fundermax) to the industry as a whole, you will recognize that at Fundermax, sustainable manufacturing is part of the ethos of the company.
Consider that back in 2005 – well ahead of the rest of the industry – Fundermax had already reduced its carbon emissions by 30% by minimizing the use of fossil fuels and is on target for net-zero.
What is a Health Product Declaration (HPD)?
In conjunction with the EPD, another document to consider is the Health Product Declaration (HPD). This is a document manufacturers use to disclose product ingredients and any health hazards associated with them. It is fair to say that architects and designers are paying more attention to the health impacts of buildings, including possible health impacts of building products. In order to get beyond the generic safety assurances from product manufacturers, designers are wisely asking for more information about what is actually in products.
To encourage greater disclosure of building product ingredients, a variety of people in the green building movement came together to create the HPD format. The HPD has been recognized in the LEED and WELL rating systems, and the HPD has begun to influence how designers select building products.
The HPD should not be confused with the MSDS (Material Safety Data Sheet) or globally harmonized SDS (Safety Data Sheet). The SDS, for instance, only provides a list of certain hazardous ingredients and is required by law for chemicals that will be handled by workers in factories or on jobsites. The SDS is designed to help medical professionals and first responders understand what they are dealing with in the event of a chemical spill or other crisis.
Health Product Declaration Standard Components
The main component of a Health Product Declaration is a list of every ingredient that is present in the finished product. For each of these ingredients, the following information is included:
-
Common name (name that the ingredient is normally called).
-
Chemical Abstracts Service (CAS) registry number: Because chemicals have many different common names, the CAS number identifies the chemical based on how it is identified in a global database.
-
Percentage the substance comprises in the finished product.
-
Role of the substance in the product.
-
Any known health hazards that regulators or scientists around the world have associated with the substance.
-
Level of disclosure (or “threshold”) in parts per million (ppm), with smaller numbers indicating a higher level of disclosure.
-
VOC (Volatile Organic Compound) data and product certifications (such as GREENGUARD certification for low chemical emissions).
-
Explanatory notes (anything the manufacturer wants you to know about the product or one its ingredients that is not part of the structured data).
Further details about HPDs can be found here.
Both the EPD and HPD help highlight important considerations to Form, Fit, and Function with a greater emphasis on the EPD providing critical data on the sustainability of the product/material. However, additional data from key tests are essential for identifying the material best suited for the scope of a particular lab. This additional data can fall under multiple test methodologies, but the point is, the independent information is out there. Material transparency is available, if only manufacturers will take it upon themselves to provide it, and if lab planners and designers know to expect it.
Material Transparency
What does that really mean?
Material transparency means the provision of independent data that architects, designers, and sustainability engineers can use to research hidden product impacts such as embodied carbon, toxic ingredients or byproducts, and social responsibility in the supply chain.
Manufacturers may release many types of documents in order to facilitate transparency, including:
-
Environmental Product Declaration (EPD)
-
Health Product Declarations (HPD)
-
Corporate sustainability reports, which look at the overall environmental impacts of a whole company
-
FSC certifications
-
Recycled Content Certifications
-
VOC certifications (such as GREENGUARD)
-
Certifications on functionality & performance (such as SEFA 3 and ASTM certifications)
-
Country of Origin
Why does it matter to a lab planner or designer?
Material transparency enables qualified material selection. For example, when selecting materials for lab work surfaces based on chemical resistance, look for the SEFA 3 independent test certificates (SEFA 3 is a 24-hour chemical test of 49 reagents on lab work surfaces). As with EPDs, SEFA 3 is an independent test, and the test houses have been approved by the governing body, SEFA (the Scientific Equipment and Furniture Association).
The current standard to pass SEFA 3 as laboratory-grade is to receive a Level 3 (objectionable change) rating on no more than four reagents. Consider that it is very easy for a manufacturer to simply state, “We meet SEFA 3.” Here though, we believe it is important to analyze the actual independent test certificate. A lab material’s suitability for a given application depends on the chemicals used in a given laboratory. By requesting the independent test certificate, you will see how the material handled each of the 49 chemical reagents. (Note that materials that pass SEFA 3 are listed on the SEFA website.)
How do you ensure material transparency?
It should be incumbent upon us, as manufacturers, to provide the independent test data to you, the professionals working to design and build sustainable labs.
But, what should you do if a manufacturer says that kind of data is not available?
Request that the material be tested and to see the resulting independent test certificates. This is not an unreasonable request, and it can help avoid potential greenwashing or mistaken information being provided.
Greenwashing (noun): behavior or activities that make people believe a company is doing more to protect the environment than it really is.
By requesting, expecting, and utilizing material transparency from manufacturers, you are well placed to move the needle on real change. Through material selection, designers and lab planners can play a pivotal role in furthering the reduction of carbon emissions.
At Fundermax, our commitment to sustainability has always been rooted in our commitment to do the right thing – and this commitment drives our push for material transparency. If you are designing a lab or reviewing options for lab work surfaces, our reps are available to discuss the unique qualities of our lab grade phenolic panels.
We have experience with various laboratory applications around the world, and our team can help support your design needs. Contact us today for more information.