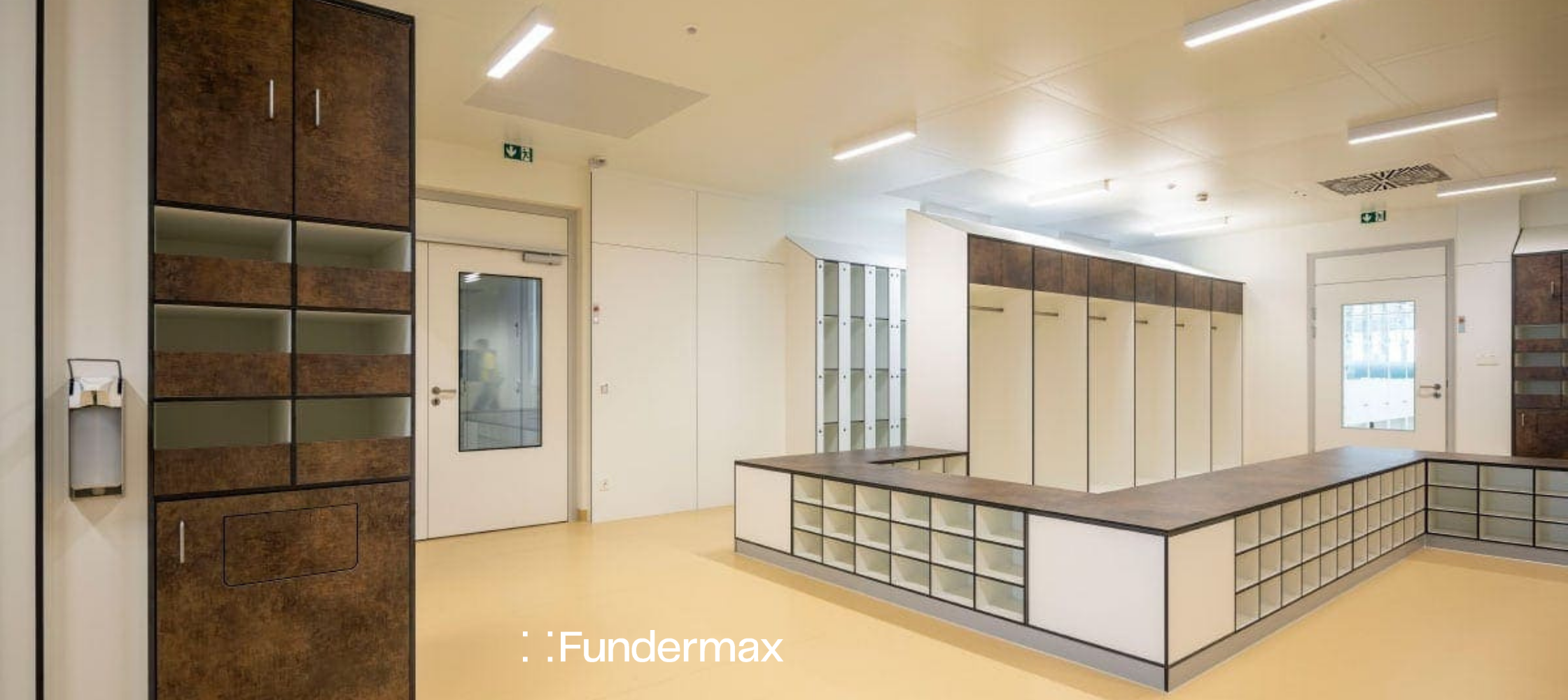
HPL Compact vs. Thin Laminate Products for Interior Applications
There are many options when choosing surface products for interior applications. But when durability, value, or customization are top priorities, the options begin to narrow. Making the right choice will depend on the amount of durability and longevity your project requires.
Architects and designers have long recognized the benefits of using high-pressure laminate panels (also called HPL or phenolic resin panels) for interior use, but even among the HPL products that are available, there are choices to make.
Here we will assess the distinctions between types of HPL panels for interior use -- specifically, the choice between HPL Compact panels vs. thin laminates laid-up on or adhered to a substrate.
Benefits of Thin Laminate Laid on a Substrate
Laminates of various types have been around since the early 1900s, and thin laminate materials became popular among consumers beginning in the mid-20th century when product advancements allowed for bright colors and wider design opportunities. The iconic laminate of the 1950s was a thin laminate laid-up on a substrate.
Not Your Grandma’s Laminate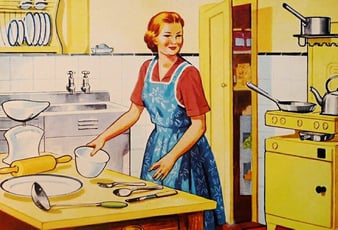
Thin laminate phenolic resin panels are less than 2 mm thick and designed to be bonded to substrates. Today’s thin laminate materials are stronger than those of decades past but the substrates and the bonding process have largely remained the same. Standard substrates include medium density fiberboard (MDF), particleboard, and plywood.
One limitation of thin laminate laid-up on a substrate is that even though the laminate surface is impact-resistant, the bonding adhesive or glue may fail, depending on the type of adhesive or glue used and how it was applied, resulting in delamination. Additionally, moisture can breach the laminated panel at the seams and edges, which can then swell and cause delamination as well. In addition, any time the laminate begins to come loose from the substrate, this creates a place where bacteria and microbes can grow, particularly at an edge condition.
Lower Upfront Cost
A notable benefit of using thin laminate laid-up on a substrate is the low upfront cost when compared to HPL compact panels for interior use. That said, in traditional thin HPL lamination, there is the cost of the decorative sheet, a glue line, a substrate, an additional glue line, a balancing backer sheet, press time, fabrication time and edge-banding. With compact laminates, the sheet is fabricated to size without any additional steps. Also, thin laminate has been a well-known and widely used solution for decades, so it is a fairly straightforward recommendation for an architect or designer to make.
It must be noted that the potential for delamination (including the likelihood of people simply picking at thin laminate panel seams), adds up to regular maintenance and/or replacement costs over time. So, while the upfront cost is likely lower than other options, the lifetime cost may be higher, depending on the demands of the environment.
Benefits of HPL Compact Panels for Interior Use
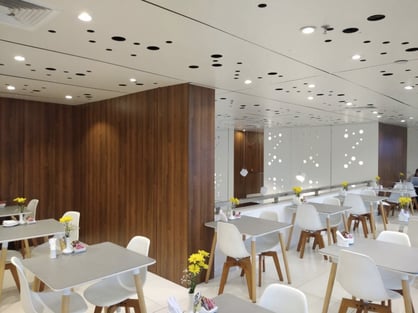
The use of compact laminate panels is on the rise for interior applications. The first distinguishing factor between HPL compact and thin laminate is that HPL compact panels have a thickness greater than 2 mm (compared to 1 mm, and even less, for thin laminate products).
For example, Fundermax Max Compact Interior phenolic resin panels are available in thickness options ranging from 2mm to 20mm, although 6, 8, and 10mm are most commonly used.
Strength and Longevity
The added thickness of HPL compact panels is the result of how the product is manufactured. compact laminates consist of a panel core that is made from multiple layers of phenolic resin-impregnated kraft paper. The outer layer, or décor layer, is printed with the color, woodgrain, material grain, or custom image that is chosen. The décor layer and core are placed in a press under high temperature and pressure to create a homogenous board.
While Fundermax’s Max Compact Interior product has a melamine impregnated décor layer, Max Compact Interior Plus also has a polyurethane acrylic coating which gives this particular HPL compact its superior impact resistance and UV resistance.
Thin laminate panels are designed to be laid-up on supporting substrates which means there is always the possibility of delamination. Compact laminate panels are self-supporting homogeneous boards; this means delamination is physically impossible.
The durability of HPL compact panels is unmatched. Compact laminates are scratch- and graffiti-resistant, non-porous and easy to clean, impervious to moisture, and does not support the growth of mold or mildew -- all qualities that make HPL compact panels ideal products for interior applications prone to high traffic and abuse.
Ease of Fabrication
As a singular, homogeneous material, it is easier to fabricate HPL compact panels than thin laminate laid-up on a substrate because there is only one material being fabricated. The thin laminate process is more complex, requiring fabrication of the substrate and laying up the thin laminate. Combining the materials increases complexity and room for error, as well as increases the fabrication cost.
Sustainability
HPL compact panels are also a sustainable choice, and Fundermax has set the bar even higher among phenolic panel manufacturers. Fundermax compact laminate panels for interior use are made with 100% recycled core paper. That means the kraft paper in the core of our interior phenolic panels is composed of 100% post-consumer recycled paper -- without compromising product performance.
Applications
Common applications suitable for both HPL compact or thin laminate laid-up on a substrate include
-
Tabletops
-
Kitchen cabinets
-
Casework
-
Wall linings
-
Office furniture
As mentioned earlier, thin laminate on a substrate has been a common choice for decades, particularly in the above applications. Today’s compact laminate panels, however, could be the stronger, longer-lasting choice.
Which is Better for Your Project?
When comparing HPL compact panels to thin HPL laid-up on a substrate, the best choice may not be the same for every project.
If you are looking for lower, upfront material cost, only need it to last for the short-term, or don’t mind maintenance and delamination repairs, then thin laminate on a substrate can be an economical solution for your project.
If you need something more durable, long-lasting, and easy to fabricate, compact laminate panels will be the best choice and provide far superior value.
As a global leader in phenolic panel manufacturing, Fundermax creates high-quality, innovative, and durable high-pressure laminates. Contact us today to discuss the best solution for your next project.