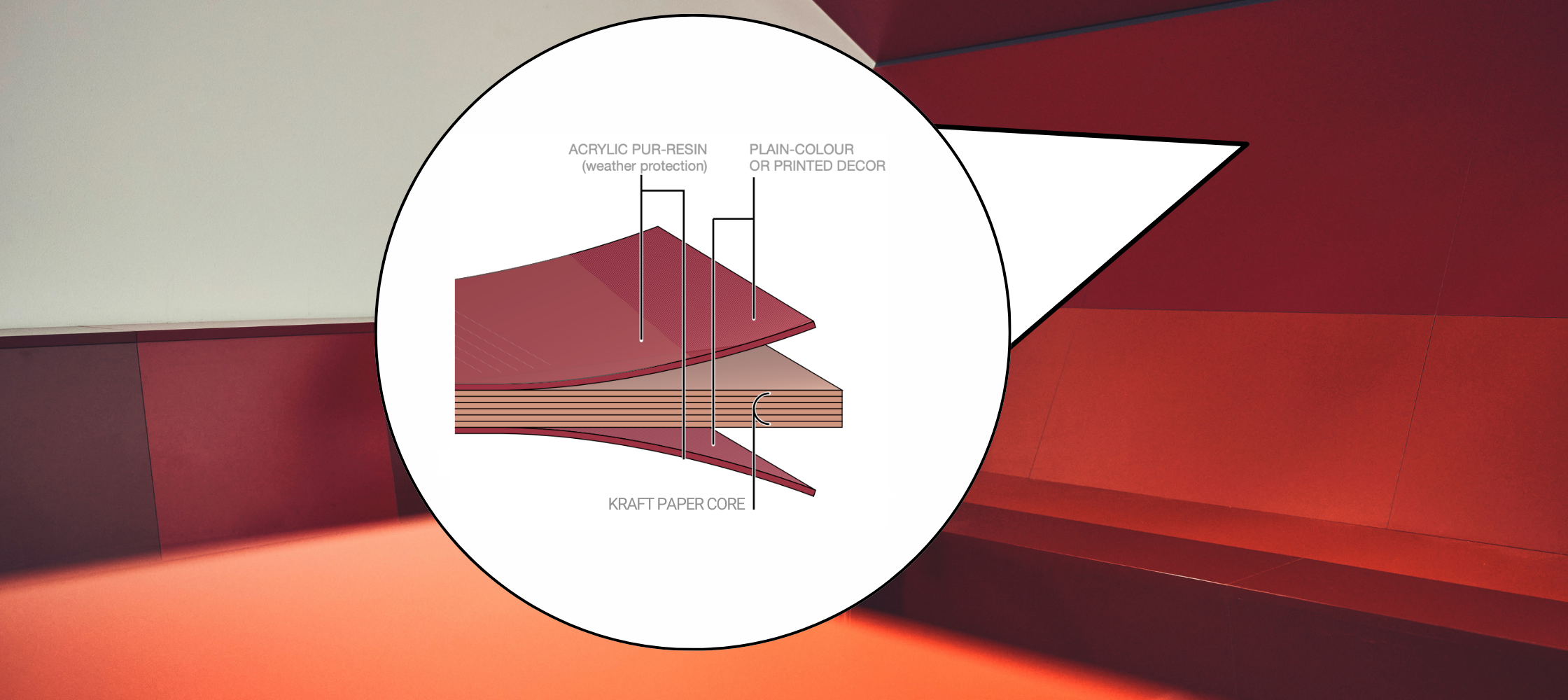
How Do They Make HPL Panels Out of Paper?
Fundermax is a global phenolic panel manufacturer for exterior, interior, and laboratory applications. We are known for our durable phenolic panels (also called high-pressure laminate or HPL panels) that are used in residential and commercial buildings, labs, universities, public facilities, and more.
Our company has been around for more than a century and as a globally trusted, sustainable brand, we hear a lot of good questions from architects and designers around the world.
One such question is, “How do they make HPL panels out of paper?” This question is usually followed closely by, “Wait. Does kraft paper swell?”
If you’ve heard that phenolic panels have a kraft paper core, you are right – which makes these questions perfectly warranted. (A paper core? How does that work?)
We are so glad you asked. Let’s start at the beginning.
How Are HPL Panels Made?
1. Kraft Paper
This specially selected core paper meets strict parameters for color, weight, and tear strength. The long fibers within kraft paper are the foundation of its strength and also allow the paper to be effectively impregnated by the resin in the next step.
2. Phenolic Resin
The core papers are impregnated with resin types known for their binding strength in order for the layers to be joined long-term. Melamine and phenol are the most important resin types in HPL panel creation. Phenolic resin is the basis of most high-pressure laminates. Phenolic resin can be mixed with flame-retardant additives; it also keeps the panel core flexible, which is essential for the bending strength of phenolic cladding panels.
3. Layers
After the core papers are impregnated with Fundermax’s precisely-calculated phenolic resin application, they are dried, cut, and placed on steel plates. The specified panel thickness determines the number of core paper layers needed. Fundermax HPL panels are made by stacking several layers of core paper and one layer of decor paper on each side.
4. Pressure + Heat
After stacking, the semi-finished panel is pressed between two heated press plates. Thermo-setting with symmetric pressure and consistent heat guarantees an appropriate joining of the resin-impregnated paper layers and creates strong, irreversible bonds that contribute to the phenolic panel's durability.
Why Our Kraft Paper Core Doesn’t Swell
But, wait? Does kraft paper swell?
That is a very good question, and the answer lies in the chemical reaction that takes place during thermo-setting. When cured, the chemical makeup of Fundermax’s specially formulated resins that impregnate the kraft paper results in a nonporous material, protecting the kraft paper core from swelling or being damaged. It is physically impossible for water to soak into our phenolic panels.
Because our panels are nonporous, they are impenetrable to certain things (like water or moisture) that may commonly damage other types of panels. The importance of nonporous materials can vary depending on the application, so not all phenolic panel manufacturers make it a priority. However, all Fundermax phenolic panels are nonporous.
Nonporous materials are especially important for lab work surfaces to ensure that germs, bacteria, and chemicals don't penetrate the surface and compromise the panel. This is of course also highly important for high-moisture interior applications as well as exterior applications to ensure that water, dirt, debris, chemicals, and graffiti don’t compromise the panel surface, strength, and durability.
How HPL Panels Are Durable
Because of our proprietary resin formula, we’re able to provide a nonporous, weather-, UV-, and chemical-resistant material that does not chip, peel, or delaminate. The kind of wall panel longevity offered by HPL panels is rooted in the durability and low maintenance of the material.
The graffiti-, scratch-, and weather-resistance of phenolic cladding panels combined with the durability to withstand harsh cleaning when necessary, result in high wall panel longevity with low maintenance.
How Testing & Code Compliance Provide Peace of Mind
The phenolic panels Fundermax offers have been tested rigorously and comply with many code requirements to provide clients the added peace of mind of local and national code compliance. "Fundermax has always set an example for market education regarding the various technical parameters of code compliance and building occupant safety,” reflects Fundermax North America’s Technical Director, Paul McCafferty.
Although only a few tests are actually required by IBC Code for HPL panels, we stand by our products so much that we voluntarily put them through extra testing – further showcasing just how impenetrable our panels are – in order to offer architects, contractors, and building owners added peace of mind when choosing Fundermax products.
.png?width=436&name=Sustainability%20Comparison%20Chart%20%20(5).png)
The phenolic panel code compliance and testing efforts are only one piece of the overall effort to provide the highest quality high-pressure laminates. Fundermax also takes an integrated management approach with four ISO certifications supporting the high caliber of our work.
Fundermax is also ahead of the curve regarding material transparency and our ability to provide an Environmental Product Declaration (EPD) Certificate as well as a Health Product Declaration (HPD).
The chart to the right highlights the main sustainability features and certifications of Fundermax high-pressure laminate panels, providing further peace of mind.
Bottom line: phenolic panels are nonporous and impenetrable by moisture. If you think this durable material could be the right solution for your next project, we would love to help. Contact Fundermax today to discuss how our high-pressure laminate panels can work for you.