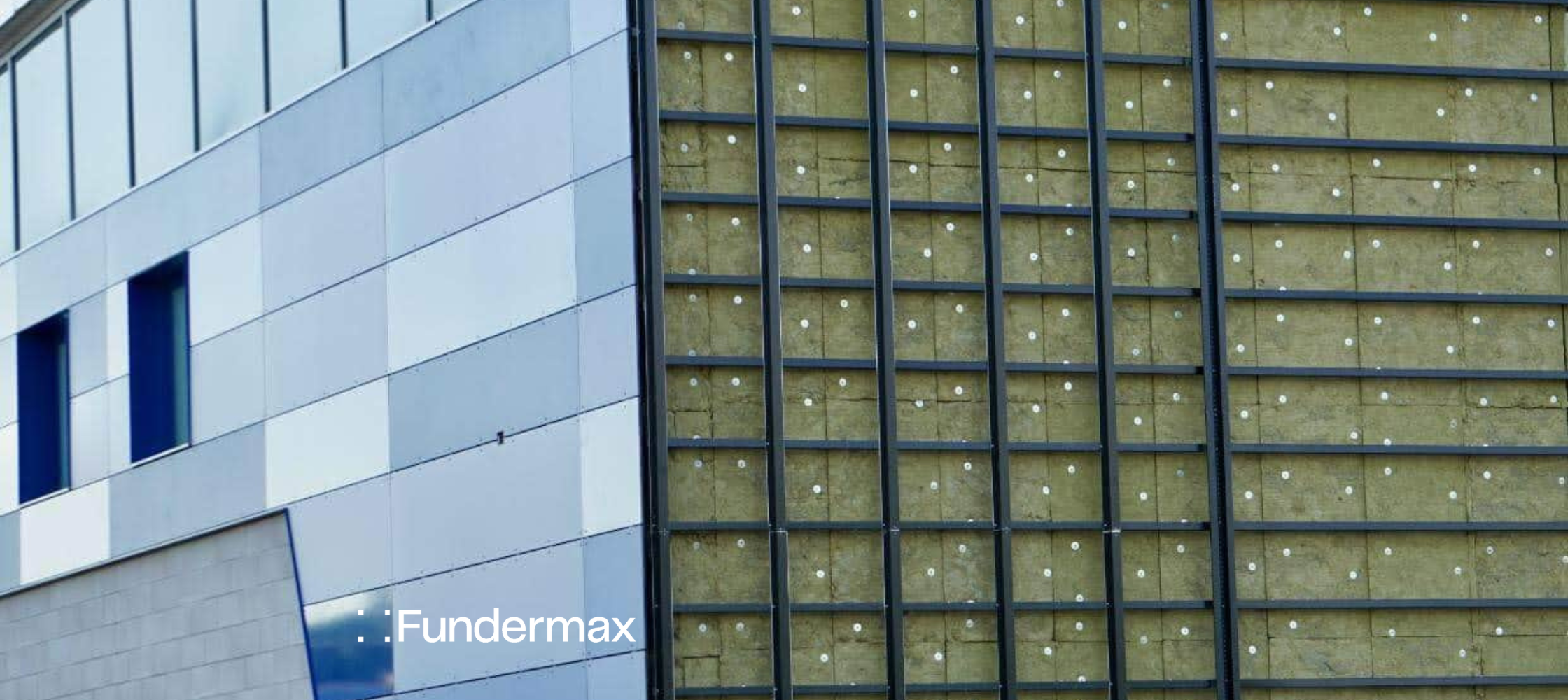
How Phenolic Panels Benefit Contractors
Phenolic panels (also called high-pressure laminates or HPL panels) are rising in popularity among virtually everyone involved in the design and building process. From architects and designers to contractors and building owners themselves, the versatility, durability, and sustainability of HPL keeps this material at the top of the list for a wide variety of exterior and interior applications.
Note that, since the basis of most high-pressure laminates is phenolic resin, the terms HPL panels and phenolic panels are used interchangeably. Phenolic panels can be used for a wide variety of applications including wall lining, rainscreens, soffits, balconies, furniture, lockers, and washroom partitions.
We realize all of these applications come with a variety of solutions, so we’ve compiled a few key reasons why contractors should choose phenolic panels. First, let’s answer a couple of common questions.
How Are Phenolic Panels Made Out of Paper?
To make HPL panels, we begin with kraft paper that has been impregnated with thermosetting resins. Then, we use high pressure and heat to compress kraft paper layers and outer decorative layers. This curing process results in solid, compact architectural boards that are durable, long-lasting, and virtually maintenance-free.
You may ask, how is that possible from a product made with paper?
The key is in the chemical reaction caused by the curing process. When cured, the chemical makeup of Fundermax’s specially formulated resins results in a nonporous material, protecting the kraft paper core from damage or swelling. It is physically impossible for moisture to penetrate our phenolic panels.
Not all applications require moisture-resistance, though, so not all phenolic panel manufacturers make it a priority. However, all Fundermax phenolic panels are nonporous and impenetrable to moisture and other impacts that may commonly damage other types of panels.
How Durable Are Phenolic Panels?
Phenolic cladding panels are made for ultimate durability throughout the life of the material – including during installation. The same weather-, graffiti-, scratch-, and impact-resistance that allows phenolic panels to endure harsh and high-traffic environments also allows for less onsite damage and breakage while installing.
For example, let’s compare phenolic panels to fiber cement or metal cladding. HPL will not chip, scratch, dent, or show damage from onsite installation activity. Fundermax phenolic panels in particular even go above the norm: the polyurethane acrylic surface of our Max Compact Exterior phenolic wall panels is 5x thicker than comparable products from other phenolic panel manufacturers.
Four Benefits of Fundermax Panels to Contractors
1. Ease of Installation
Installing phenolic panels is definitely not an amateur DIY project, but one of the clearest benefits of phenolic panels for contractors is the simple and straightforward installation.
Fundermax phenolic panels:
-
can be installed on a wood, steel, or aluminum substructure.
-
can be mounted horizontally or vertically.
-
offer four types of fastening systems (Modulo, Scaleo, exposed, and concealed).
For a detailed look at how to install phenolic panels, see this article.
2. Install Costs
Many factors can affect installation costs, which is another reason why contractors should choose phenolic panels.
Consider:
-
Fundermax phenolic wall cladding panels arrive ready for installation which means less waste and better use of your materials budget.
-
Easy installation means you save on labor costs.
-
Panel durability means you don’t have to worry about wasted materials caused by job site accidents or breakage.
Additionally, panel longevity and Fundermax’s industry-leading warranty (which covers labor) means:
-
install costs will only need to be considered once.
-
maintenance costs will be minimal.
-
replacement costs will be virtually irrelevant.
3. Ease of Fabrication
Our factory can fabricate the panels for your project, which means that when the materials arrive on a jobsite, they are ready to install without modifications. However, we know that things happen in the field, and often timelines are tight.
Since Fundermax panels do not chip, scratch, or dent, the panels allow you to:
-
make field cuts onsite.
-
use traditional woodworking tools in the field.
-
make revisions and custom cuts onsite without compromising the material.
Proper tooling requirements for Fundermax panel installation are provided in this document.
4. Panel Yield
High panel yield means less construction waste and less wasted money, and Fundermax is committed to helping you achieve the best panel yield possible. This is partly to maximize your investment in materials, and it’s also because of our commitment to sustainability.
How do we achieve high panel yield?
-
We offer four different panel sizes, which allows for greater flexibility.
-
Greater flexibility means greater opportunity to maximize the yield of every single panel in a design -- and that means the budget goes further.
-
From pattern directionality to complex color design elements, when these size options are factored in from the start, a Fundermax phenolic wall panel system offers maximum design freedom.
Installation Example: Modulo
Watch as we install phenolic panels using our Modulo fastening system in our North American showroom located in Charlotte, NC.
As one of the world’s most trusted phenolic panel manufacturers, Fundermax is committed to providing the highest quality service and products. But, we know you have a number of manufacturers to choose from.
To help, we’ve compiled a comprehensive eBook comparing Fundermax panels to others on the market. Download it for your own use here.