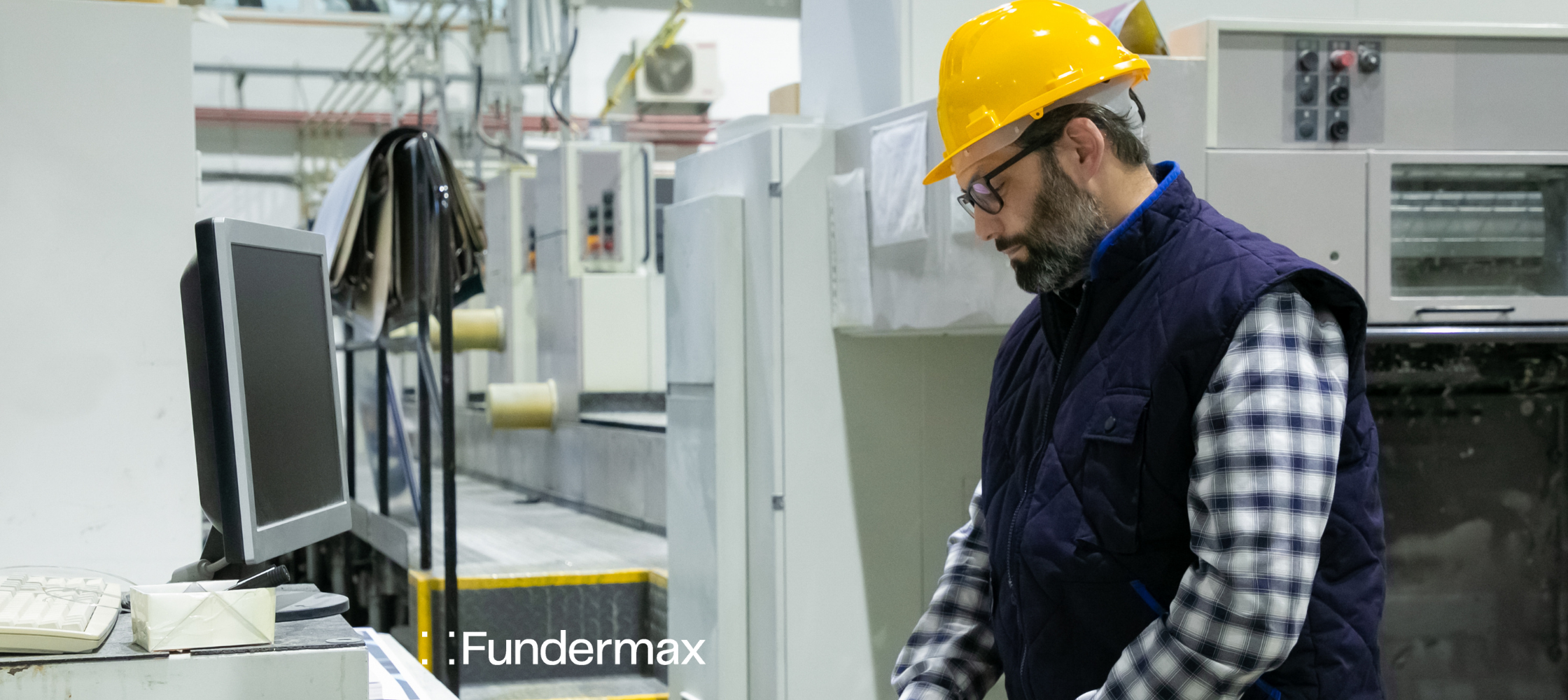
How Are High-Pressure Laminate (HPL) Panels Made?
High-pressure laminate panels (also called HPL panels or phenolic panels) are made using high pressure and heat to compress layers of kraft paper and other binding agents into solid compact boards.
As a globally trusted phenolic panel manufacturer, Fundermax has been in the industry for over a century, and while we’ve seen more people become familiar with what HPL panels are, many still wonder, “How are HPL panels made?”
With our amount of experience, we love to answer this question -- it’s what we do every day.
How Are Fundermax HPL Panels Made?
Fundermax panels are made by compressing kraft papers and binding resins using high pressure and heat. The resulting product is an industry-leading phenolic panel creation.
1. Paper + Resin
Phenolic panel creation begins with specially selected core paper that meets strict parameters for color, weight, and tear strength. This type of paper is called kraft paper. The long fibers within the paper are the foundation of the kraft paper’s strength, and these fibers allow effective impregnation with resin.
To be able to join the core paper layers long-term, they are first impregnated with resin types that are known for their binding strength. Melamine and phenol are the most important resin types in HPL panel creation.
The basis of most high-pressure laminates is phenolic resin. Phenolic resin keeps the panel core flexible, is essential for the bending strength of the boards, and can be mixed with flame-retardant additives. The core papers are impregnated with a precisely calculated application of phenolic resin; the freshly impregnated paper is then dried, cut, and placed on steel pallets.
As implied by the name, the decorative layer, or decor paper, determines the decor of the HPL panel. Many different designs including solid colors and prints are available, and even the finest wood grains can be displayed with high resolution.
The décor paper resins play a significant role when it comes to the durability of the surface, including scratch- and abrasion-resistance. Like the core papers, the decor papers are impregnated with décor paper resins and then dried, inspected, and cut.
The core paper and decor paper are now ready for stacking.
2. Layer + Stack
Fundermax Max Compact boards are made of several layers of core paper and one layer of decor paper on each side. The thickness of the board determines the number of core paper layers needed.
For example, to produce a 1mm-thick HPL panel, 2-3 paper core layers are required. In comparison, 6mm-thick Fundermax panels are made using approximately 24 core papers.
We begin by stacking the layers of the compact board on a press plate. The press plate is responsible for the surface of the board and provides the requested structure/texture and gloss. The layers are precisely positioned in order to ensure optimal usage of the press plate and to prohibit trim waste.
First, a layer of decor paper is placed on the press plate. Next, a layer of precisely-counted core papers; then, a final decor layer is placed on the top of the panel stack. Now, the paper stack is ready for pressing.
3. Pressure + Heat
After stacking is complete, the semi-finished board goes into the press between two heated press plates. Symmetric pressure and consistent heat are required to guarantee an appropriate joining of the impregnated paper layers. This thermo-setting creates strong, irreversible bonds that contribute to the durability of high-pressure laminates.
To ensure a perfect result, Fundermax panels are made using a regulated temperature sequence and hydraulic plungers to evenly allocate the compression during the HPL panel creation. Depending on the pressing sequence, the process takes about 30-90 minutes.
4. Inspect + Trim
Before leaving the press, the phenolic panels are cooled. Next, the boards are trimmed and then both sides of the board are given a thorough visual examination. Finally, the HPL panels are labeled, stacked, and ready to be packed for shipment to the customer.
Common Questions About HPL Panels
What is kraft paper?
Kraft paper gets its name from the German word kraft, meaning strong, and is made using the Kraft process. The Kraft process involves the chemical conversion of wood into wood pulp using a solution of sodium hydroxide and sodium sulfide as the liquor in which the wood is cooked to loosen the fibers.
Why must the fibers be loosened? The structural components in wood are lignin and cellulose, but lignin does not make a good paper. This means the lignin must be separated from the cellulose. To do this, the Kraft method cooks wood chips in a solution of sodium sulfide and sodium hydroxide to break apart the lignin and cellulose.
This method produces wood pulp with a reduced lignin content and high sulfur ratio, distinguishing itself from other paper production methods because the resulting kraft paper is stronger than paper produced by other methods.
Are all phenolic panels made the same?
The overall makeup of high-pressure laminates is similar between companies, but different phenolic panel manufacturers have their own processes and make their panels differently based on application, markets, and costs.
Higher quality panels will have more durable, integral acrylic surfaces with no risk of delamination. Lower quality panels will use after the fact applied acrylic films which can have issues over time depending on the application.
One of many unique features of how Fundermax panels are made is our in-house resin station where we mix and prepare our own resin formulas. This allows us to achieve the desired quality of chemicals to ensure an industry-leading product that meets all of our high standards. Fundermax owns several patents on the technology we use on our NT surface for Max Exterior panels.
Are HPL panels sustainable?
Yes. Most HPL panels are sustainable in some way, regardless of the manufacturer. Fundermax places a great priority on sustainability and has continued to raise the bar in our industry. Read more about sustainable phenolic cladding panels here.
Are HPL panels durable?
Yes. HPL panels are made for ultimate durability, including weather-, chemical-, and abrasion-resistance. Read more about the durability of phenolic wall panels here.
Are HPL panels code compliant?
Yes, but the extent depends on the manufacturer. Some phenolic panel manufacturers are code compliant with just what is minimally required. However other manufacturers, like Fundermax, go beyond what is required in their HPL panel creation. Read more about phenolic panel testing and code compliance here.
Fundermax panels are made for a wealth of applications, from solid exterior phenolic wall panels to thinner decorative HPL plates placed on carrier materials.
While overall, HPL panels are made from a common framework, in order to ensure you select high-quality phenolic wall panels, make certain you work with highly reputable and globally trusted phenolic panel manufacturers like Fundermax.
Contact us today to see if a phenolic wall panel system may work for your next project.