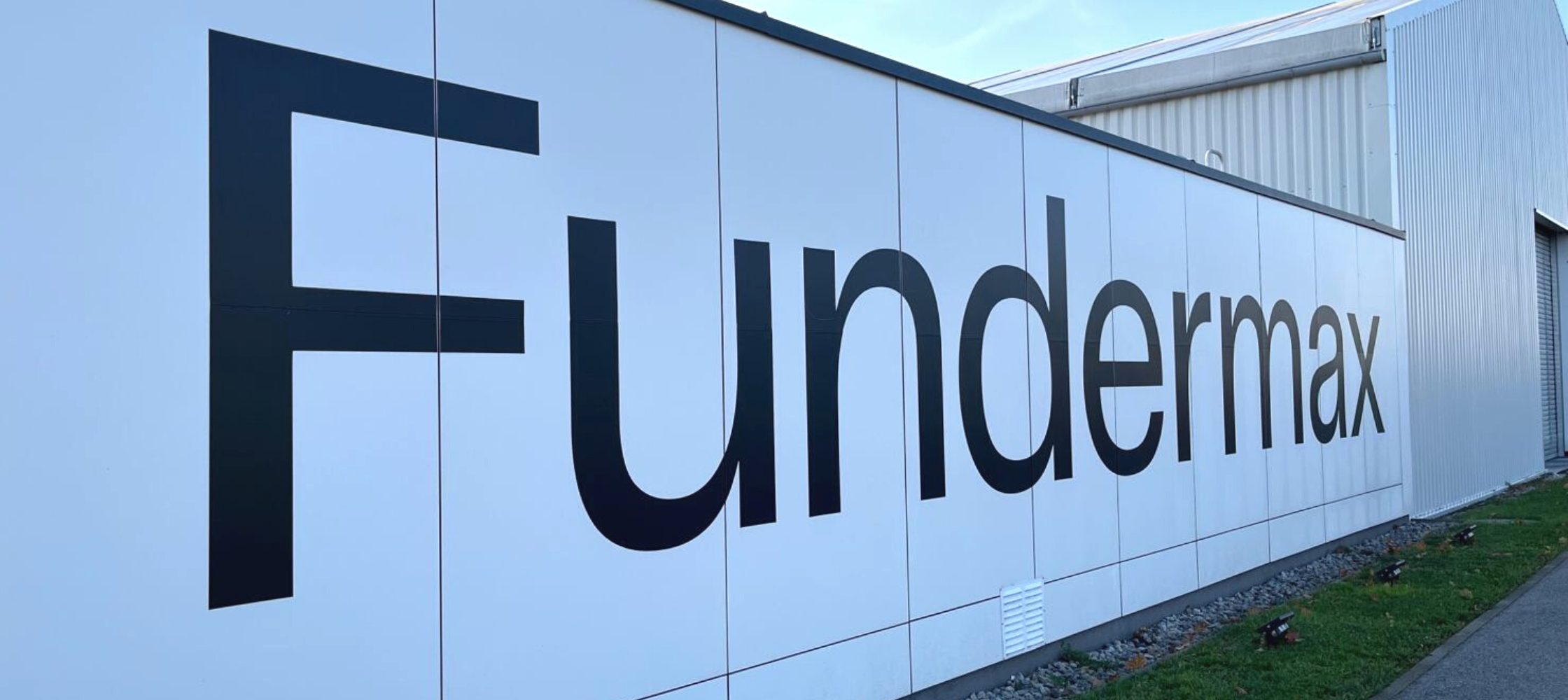
The History of Fundermax
Fundermax is a global leader among phenolic panel manufacturers. With a history that is more than a century-long and many locations all over the world, we remain committed to providing the best products, service, and support in the industry.
Fundermax has been working with precision and love for natural raw materials for over 130 years. Today, we are a manufacturer of high-quality, wood-based materials and the world market leader for compact laminates for both interior and exterior applications. Fundermax stands for top quality and excellent design.
Our goal: To provide customers with the best possible support in realizing their ideas. We are part of Constantia Industries AG and thus belong to one of the largest privately-run industrial groups in Austria.
In this blog, learn about the history of Fundermax and we came to be one of the top global manufacturers of phenolic panels, with seven different products, ten global offices, around 1,400 employees worldwide, multiple manufacturing sites, over a hundred different decor options, and more.
The History of Fundermax
Beginnings
The Fundermax story began in the Austrian lumber industry in 1890 when Karl Funder invested in his first sawmill. His drive to innovate in globally beneficial ways led Funder to the industrial production of the first wood fiberboards. In 1943, Funder founded the first wood fiberboard plant in St. Veit an der Glan, Austria, where Fundermax remains headquartered today.
Meanwhile in 1896, Belgian-American chemist Leo Hendrik Baekeland had begun experimenting with making laminate sheets and, in 1907, Baekeland patented a product named Bakelite. The Bakelite material was composed of sawdust and wood fibers that were combined with phenol resins and then pressed into metal forms and cured by heat; the first thermosetting plastic was born. Bakelite technology is ultimately the basis of all HPL. The phenolic resin sheets became some of the first insulating material, the likes of which you will find when you open an old transistor radio.
Early Days
Up to this point, HPL was used strictly for technical and practical purposes devoid of any decorative aspects. But in the early 1950s, companies like Formica and others began to introduce decorative thin laminates as a more durable alternative to wood for kitchens and furniture. Meanwhile, Fundermax (which were two separate, competing companies at the time: Funder and Isovolta (whose decorative laminates brand name was ‘Max’)) was also manufacturing thin laminates. Since 1948, we had made thin HPL sheets primarily for laminated boards for kitchens, tables, and other furniture where a durable surface was useful.
Then in the 1960s, Fundermax received its first requests specifying a slightly thicker laminate (3mm or so rather than 1mm) for train and tram renovations. The thicker laminate, also called self supporting HPL, offered more durability and greater impact-resistance. Since Fundermax had already sold a lot of thin HPL for laminate furniture boards, we were still known primarily for thin laminates. However, our sales team and application engineers had introduced thicker HPL as impact resistant wall claddings and low maintenance and rust free ceiling elements.
When the Vienna underground began construction in 1978, they needed thicker HPL panels for the wall claddings, and we sold a lot of these HPL panels to them. For a very long time, all the interiors of the wall, cladding, and ceilings of the Vienna subway stations were made of our HPL panels.
Growing to Include Exterior Panels
The first HPL panels in exterior applications were simply interior panels with decors containing a good lightfastness and melamine resin. These were applications like balcony coverings, but not yet façades. Still, the interior panels in the exterior applications were interesting because they were very durable, impact-resistant, and easy to machine and install, even in the outdoor environment.
In the 1990s, Fundermax took notice of the growing interest in and demand for ventilated facades. So, rather than strictly staying in the lane of thin laminates, Fundermax made a clear decision to enter the exterior environment. The company was determined to create a flame-retardant, scratch- and solvent-resistant, colorfast, durable, UV-resistant panel.
Fundermax, along with competing phenolic panel manufacturers, raced to develop the best technology for exterior applications. Our application engineers determined that while our panels were incredibly strong, the colorfastness was not up to our standards. So our first step in development was adding an acrylic melamine top layer. We called these exterior panels exterior E and EP. The new top layer gave the panel a very good lightfastness, but a very bad scratch and solvent resistance. Unfortunately, acrylic melamine is very soft. We still had work to do.
Then around 1997, Fundermax developed a double-curing technology. In the first step, we coated the panel and hardened the coated paper in a drying tunnel; then, a second hardening when we pressed it. Our double-curing process was unique among the competition and produced panels that were “hard as a diamond,” as our slogan said at the time.
Next, the first Fundermax exterior phenolic panel with our NT technology was produced around the year 2000. NT is Fundermax’s patented chemical curing technology that is used to create the colorfast, durable, UV-resistant phenolic panels we had envisioned.
Individualdécor
The first Individualdécor print was a hand-drawn illustration pressed into a panel. Fundermax’s Head of Application Engineering at the time enjoyed drawing in his free time. He took a drawing he made to the factory and requested they press the design on a panel. They created the panels like normal but instead of the decor layer, they added his drawing and then the final protective layer over it… and it worked! The first custom-printed panel at Fundermax had been made.
Later, this capability was commercialized because we had demand from companies with industrial machines, control panels, and circuit diagrams that needed instructions and switch labels printed on them. We acquired technical drawings and press-laminated them into panels. It was piecework, so it was not easy; but we believed in the product, so we found a company in Vienna that still does the individual prints for us today.
Together with the printer, we discussed which kind of paper and ink would be best for this type of product. They started on a small scale, learning step-by-step doing individual prints; next, we had a collection made from artists, and then we allowed clients to send us a file of what they wanted to be printed (which was much more complicated in the early 2000s!). These first projects were all interior. Then, after much time spent finding and testing lightfast inks, we manufactured the first exterior Individualdécor project around 2007.
Today
In recent years, Fundermax, the leading specialist in central Europe for manufactured wood products and decorative laminates, has also expanded worldwide. While still headquartered in Austria, we opened new branches in France, India, and Spain between 2006 and 2012, and most recently, we launched Fundermax North America, headquartered in Charlotte, NC in 2015.
There are five plant locations in Austria producing the full range of Fundermax products including Max Compact Exterior, Max Compact Interior, Exterior Individualdécor, Interior Individualdécor, and Max Compact Interior Plus, and Max Resistance2.
The strength of Fundermax lies in our well-researched and thought-out wood-based materials and compact laminates. We operate as a production facility, a service partner, and a design laboratory. Because of our strength in all three areas, top-notch performance is a given. Fundermax continues to innovate to meet evolving market demands and is committed to providing the very best service and support in the industry.
Phenolic Panels in Action
See for yourself how Fundermax phenolic exterior wall panels have made a difference in these exciting case studies.
Ash Street Case Study
This 1500 sq. ft. residential project showcases a unique application of a phenolic panel system as a rainscreen façade on the wall as well as the roof. Read more here.
Smoky Hollow Case Study
In a district that includes office space, apartments, restaurants, and more, Smoky Hollow’s 421 N. Harrington St. offers a stunning example of Fundermax panels matching high performance with high design. Read more here.
Lockhart Stadium Case Study
Major League Soccer meets HPL panels in this exciting Florida wall panel case study featuring Inter Miami CF’s home pitch: Lockhart Stadium. In 2019, Florida architecture firm Perez & Perez was contacted about an ambitious 18,000-seat stadium with an 11-month timeline from design to completion. The team considered many materials, but exterior phenolic wall panels rose to the top of the list for their superior durability and versatility. Read more here.
From our perspective, when we sell exterior, interior, or laboratory phenolic panels, we’re not just selling the panels. We are also providing all of the testing that has gone into the product and all of the technical advice.
With our global reputation as a phenolic panel producer combined with a century of experience… this is more than just pressing a panel. This really makes a difference, and we see how much this matters to our clients in the United States and around the world.
Contact us today to see how Fundermax can make a difference in your next project.