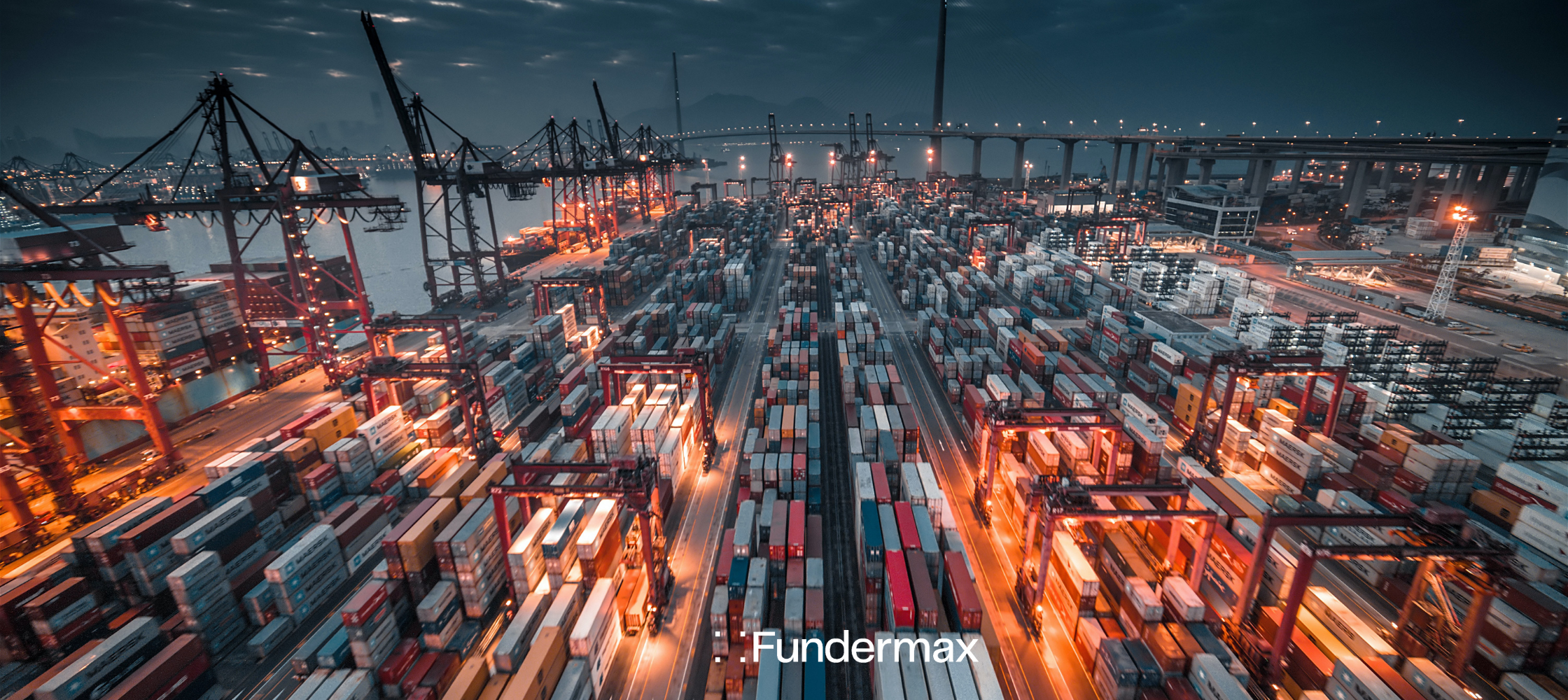
The Global Freight Crisis: A Manufacturer’s Perspective
By now you’ve most likely heard about the “global freight crisis,” “global shipping crisis,” “container shortage,” “shipping delays,” etc. -- but what does it all mean, how does it affect lead time, and when will it get better?
As phenolic panel manufacturers who serve architects and builders around the world, Fundermax is quite familiar with the universal importance of project timelines, manufacturing lead time, and construction deadlines. That also means we have a front-row seat to the impacts of today’s global freight crisis.
What is the Global Freight Crisis?
One of the early impacts of COVID-19 was the disruption to supply chains around the world. What began as a “disruption” has matured into global shipping delays, or rather, a full-on global shipping crisis.
A combination of pressures including a shipping container shortage, port traffic backups, and labor shortages has created the perfect storm, resulting in a crisis that, according to manufacturers and shipping executives, is going to get worse before it gets better.[1]
Adding to the pressure, consumer demand is even higher, and the construction industry, in particular, has continued working endlessly. This has even further increased the demand for manufacturers to get their products to consumers ASAP.
How Does a Freight Crisis Affect Lead Time & Costs?
Throughout the pandemic, the demand for our phenolic cladding panels has remained high; and, while keeping pace with the manufacturing demand, we continue working to keep production times as low as possible.
However, as is the case across industries worldwide, not all factors that affect lead time are within a manufacturer’s control. It is always wise to consider how various factors can impact lead time and costs -- and even more so during a global shipping crisis.
But, how exactly do shipping delays make such a great impact on manufacturing lead time and costs? There are three key factors that, as you will see, actually overlap and compound one another.
Container Shortage
One factor causing global shipping delays is a container shortage. Manufacturers around the world are having to wait for shipping containers to become available.
But, why is there a container shortage?
The reason is multi-faceted. In the early days of the pandemic, manufacturers were unsure of how consumer behavior would respond, and shipping container use actually fell temporarily.
However, according to Steve Saxon, a partner with McKinsey & Company, “By the middle of 2020, it was pretty clear demand was going to be robust. All those container ships were sailing again.”
In only a few months, the shipping industry was functioning at full capacity, with 97-98% of container ships running at all times.[2]
Here, the limitations of the situation became apparent. At the same time that customer demand soared and shipping containers hit max capacity, there became a shortage of dockworkers and truck drivers.
This labor shortage (touched on further below) led to containers taking longer to be unloaded, meaning they were not always available to be shipped back. These complexities have resulted in empty containers accumulating at some ports while remaining scarce at others.
Like other manufacturers around the world, as soon as a container is available, Fundermax packs it up with as many orders of phenolic cladding panels as we can for shipment.
Shipping Wars
Once a manufacturer has filled a container, the next part of the crisis they face is getting that container onto a ship. With such high demand, the space on container ships has become scarce. This is the factor that impacts cost as much as -- even more than -- lead time.
In August, CNN Business reported that the World Container Index of Drewry (a maritime research consultancy based in London) showed the composite cost of shipping a 40-foot container on eight major East-West routes was up 360% from a year ago.
Why exactly are freight rates skyrocketing, though?
According to Maersk CEO Soren Skou, "The current historically high freight rates are caused by the fact that there is unmet demand… There’s simply not enough capacity.”[3] Philip Damas, head of Drewry’s supply chain advisors, explained to Global Trade Magazine, “Now everything is overbooked. Shippers are desperate to book… It’s more a bidding war than it is a traditional tariff, and this bidding war is accelerating.”
Labor Shortage
Once a container is on the ship, it will travel by sea to its next destination. In our case, the container of phenolic cladding panels will sail to one of the two main ports we ship to (Charleston and Los Angeles).
That, however, becomes the next point of delay, given the congestion at ports all over the world, particularly in Asia, Europe, and North America. Bob Biesterfield, CEO of C.H. Robinson, told CNN Business, “The chances of your vessel arriving on time are about 40% when it was 80% this time last year."
Worldwide, hundreds of container ships are bottlenecked at overloaded ports. On Sept. 14, Business Insider reported an all-time high of 56 container ships anchored offshore and waiting to access California ports.
Why the bottleneck?
As mentioned earlier, the labor shortage is a huge part of the problem. The pandemic and its restrictions have limited the availability of dockworkers and truck drivers, causing delays in handling cargo in every step of the process. A container that can’t be unloaded in one place is a container that can’t be loaded somewhere else (further compounding the container shortage).
Here, we reach the final leg of the journey: ground transportation.
Even after being unloaded from the ship, without truck drivers, the bottleneck persists as ports are full from having to store containers while they wait for an available truck driver to transport the container.
For our Fundermax container, once the truck delivers the container to one of our two main warehouses in North America (in California or Tennessee), the phenolic panels will be shipped out to their ultimate destination on an order-by-order basis.
This step involves another segment of ground transportation delivery and potential further impact of truck driver shortages.
When Do Experts Think Things Will Return to Normal?
Simply put: no one is sure. There really is no quick fix to this issue, and the impending holiday increase in consumer demand will only further increase the pressures.
As reported by Bloomberg.com, Karsten Michaelis, head of ocean freight at DHL Global Forwarding Asia Pacific, states, “We do not expect freight rates to stabilize in the near term… The combination of a year of disruption, lack of containers, port congestion, and a shortage of vessels in the right positions is creating a situation where cargo demand far exceeds available capacity.”
So, what should you do?
The two most important adaptations for consumers and purchasing managers during this time are to order products as soon as possible and be patient.
Remember: many factors contributing to and resulting from the global shipping crisis are completely out of everyone’s control. Manufacturers are just as frustrated as consumers and are working to speed things up in any way possible. Patience and understanding are key, as well as ordering early.
For Fundermax orders specifically, the sooner an architect connects with a company representative, the better the process will be. Our product experts can help make sure everything is correct in the blueprint stage so orders can be placed ahead of time, allowing you to still meet deadlines.
If you are considering a phenolic wall panel system for your next project, contact us today for more information.
[1] https://www.bloomberg.com/news/newsletters/2021-08-26/supply-chain-latest-global-shipping-snarls-to-linger-to-2022
[2] https://www.voanews.com/a/economy-business_no-quick-fix-shipping-crisis-creating-supply-chain-bottlenecks/6210070.html
[3] https://www.cnn.com/2021/08/23/business/global-supply-chains-christmas-shipping/index.html